I am fed up with the kit supplied peanut tank, looks cheap and store-bought! (I think I actually just read that somewhere recently)
I took a trip down to the local motorcycle salvage. After speaking with the owner and finding the smaller fuel tanks, I chose this one
It belonged to a Yamaha JT-1 from the 1970's...
I noticed the light surface rust inside before purchasing and was not bothered by it a bit. OOPS!
Of course, after wire brushing the whole tank... I find about 50 total holes, after cleanup it looked more like a strainer. I didn't expect this but, I figure I can deal with this since they're not bad and I think of myself as a resourceful person...
So this is what I ended up with, rolls of copper set into the holes as a filler to help the solder fill the holes.
I found that meticulous cleaning and preparation of the area to be worked helps a lot. Flux is the answer though, heat the surface with a torch and apply some flux. Heat the surface again and repeat, when the flux starts evaporating from the metal... apply the solder to the copper filler in the hole and melt some solder to it. You should see this hole and the copper start to suck the solder into the tank. When you see this, add more solder to the edges and make sure you have a solid connection between all of the metals. Grind down with a rasp/file and sand with a foam block or paper. Viola... DONE!
I took a trip down to the local motorcycle salvage. After speaking with the owner and finding the smaller fuel tanks, I chose this one
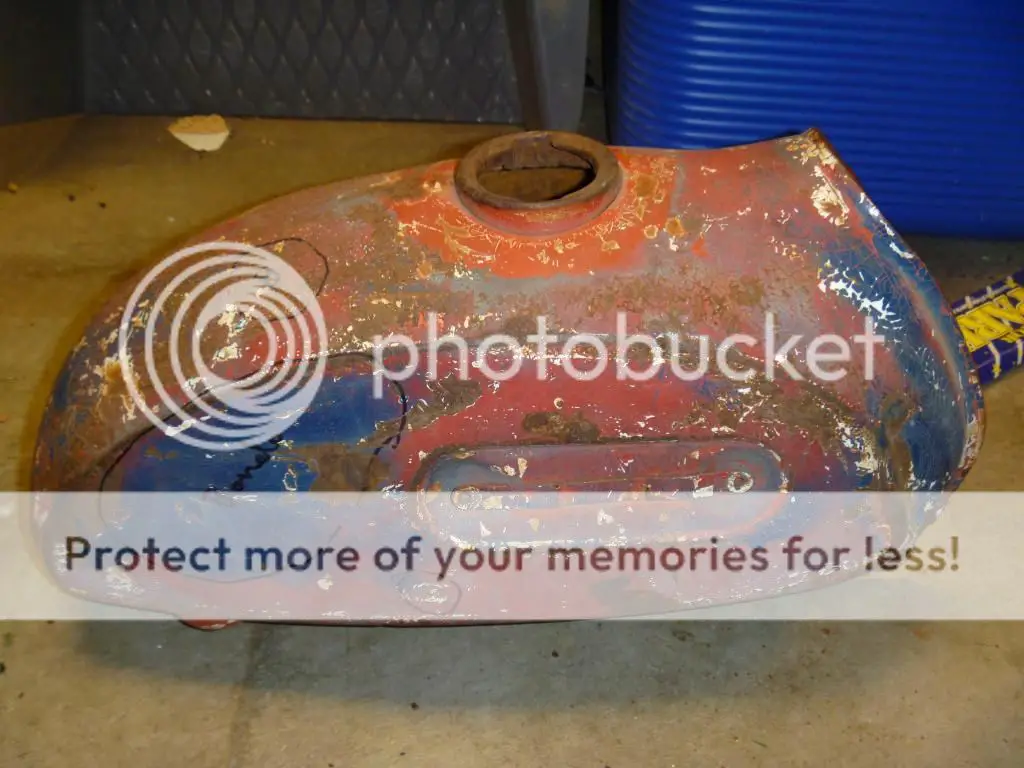
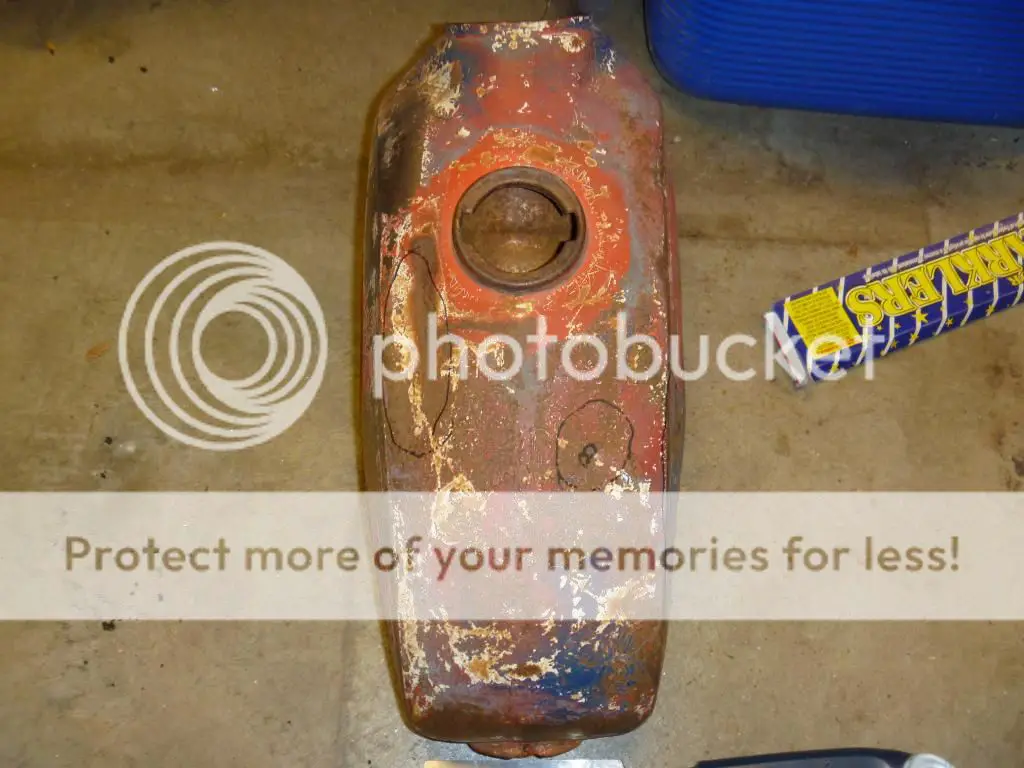
It belonged to a Yamaha JT-1 from the 1970's...
I noticed the light surface rust inside before purchasing and was not bothered by it a bit. OOPS!
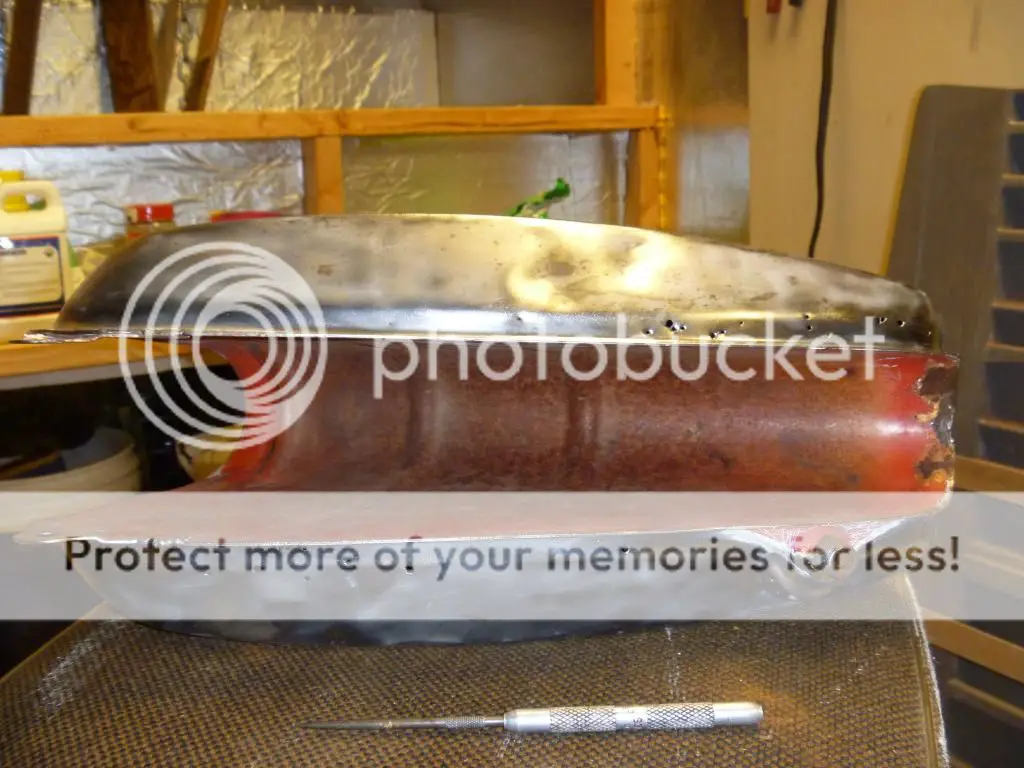
Of course, after wire brushing the whole tank... I find about 50 total holes, after cleanup it looked more like a strainer. I didn't expect this but, I figure I can deal with this since they're not bad and I think of myself as a resourceful person...
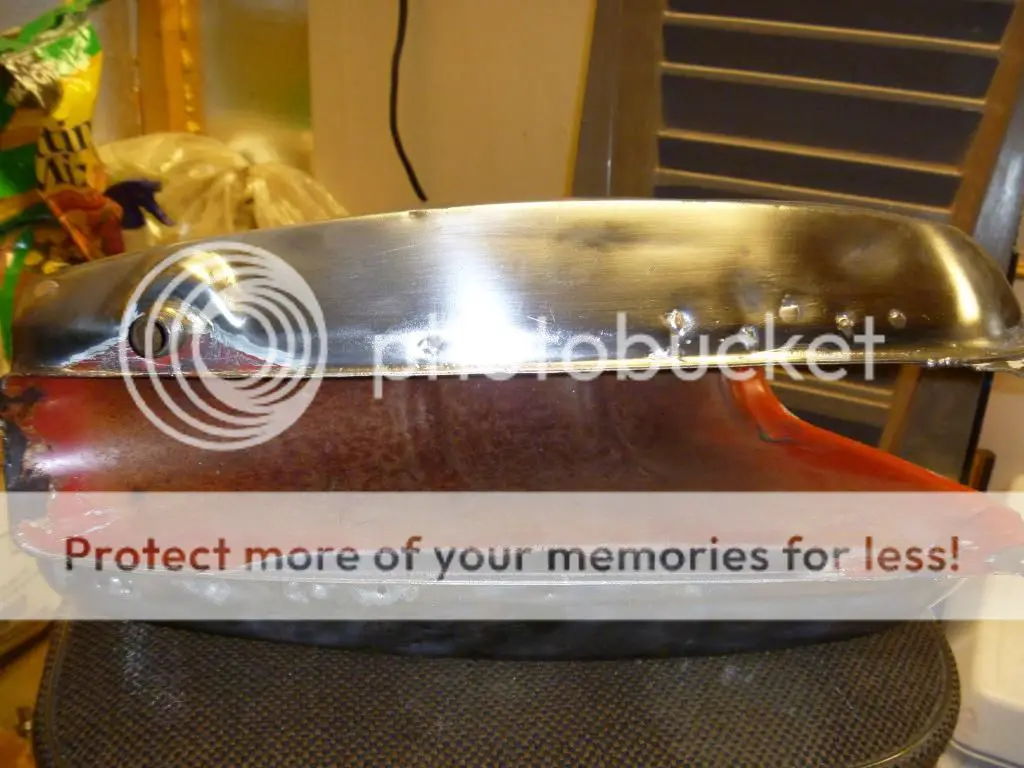
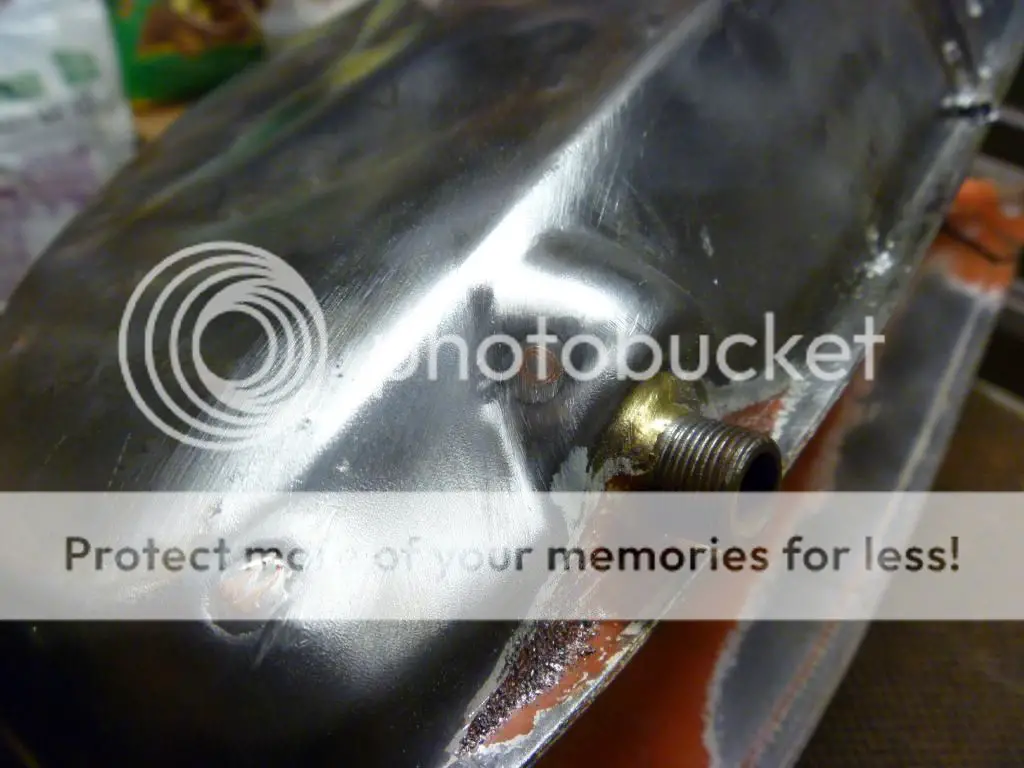
So this is what I ended up with, rolls of copper set into the holes as a filler to help the solder fill the holes.
I found that meticulous cleaning and preparation of the area to be worked helps a lot. Flux is the answer though, heat the surface with a torch and apply some flux. Heat the surface again and repeat, when the flux starts evaporating from the metal... apply the solder to the copper filler in the hole and melt some solder to it. You should see this hole and the copper start to suck the solder into the tank. When you see this, add more solder to the edges and make sure you have a solid connection between all of the metals. Grind down with a rasp/file and sand with a foam block or paper. Viola... DONE!