Well Fasteddy got to staring at the box of bits that went up to the machinist who was always going to do it next week. Perhaps unfortunately, creative staring became creative doing. Always a frightening and upon occasion, terrifying, thought around our house.
Here's how it happened but first, when I mention with 1" tubing and 1" pipe there is a difference.
Pipe is measured on the inside and has a thicker wall and tubing is measured on the outside diameter and comes in 1/6" or 1/8" wall so when I mention pipe or tubing that's why.
Now how I did it. When it came time to drill a hole in the pipe my little machinist vise had a hard time holding it due to the diameter so it was necessary to come up with something that would work. I took a short piece of 2x4 and screwed it to some scrap 3/4" plywood. Then the pipe went next to that and then another short piece of 2x4 was clamped to the whole thing. Then that piece of 2x4 was screwed to the plywood so it couldn't move. Used the 2x4's as a guide to measure the middle of the pipe and center punched it after measuring down from the top of the pipe to find where the center point was..
I used a metal cutting hole saw to cut the holes and made sure that there was full contact with the blade to make sure that it was centered. If there wasn't a perfect circle when it made contact with the pipe it wasn't dead center.
I bought some heavy walled 1" tubing to extend the steering on the tricars. It has a 3/4" inside diameter and has been a life saver any times. Used an 1-1/2" piece to use as a shoulder to mount the axle on the spindle. I was working on the mortise and tenon joint used with furniture where if you make a socket joint it has a lot more strength that something that is surface mounted.
The tubing and the bolt for the axle had to be fish mouthed to clear the king pin as it went past. I drilled two holes in the tubing so it could be rosette welded to the axle and then it was welded around the fish mouth to hold the axle in the tubing. To make sure it would clear I pushed a short length of the tubing up inside and used the hole to judge just where the fish mouth was in relationship to where the king pin would go. Then I welded the tubing to the pipe on the outside. The weld on the fish mouth required some light grinding to clear the king pin.
Any further clean up grinding that had to be done I did with a rotary file chucked into a drill. Fortunately the weld was just in reach of the file. A half round file would work just as well.
When it was time weld the axle in I slid a short piece of tubing over the bolt and squared it up that way. It compensated for the pipe shoulder. The side to side squareness was just eye balled.
The bottom of the king pin will have a short length of tubing like the top and will be held in place with a roll pin so it can be removed at any time.
Why didn't I use the spindles from BMI? Well first there was the challenge of making my own, also as my brother just pointed out I not the sharpest cotton ball in the bag and the king pin needs a bushing to help make the steering easier than metal to metal and that would have left me with a very long, thin 5/8" king pin that may have warped and caused the spindle to bind as the king pin bent from the force and weight.
There it is. I have posted some photos of what I did and how and one of the spindles mounted. If you want to read what I wrote on some of the photos look on the right side of the photo and if it says MORE click on it and the printing will come up. You will need to do this only if there are periods after the print that is there.
The new and improved Photobucket???
As always click on the photo to go to Photobucket. Just a fast warning. The new Photobucket has decided to publish some of the pictures over and over again.
Steve.
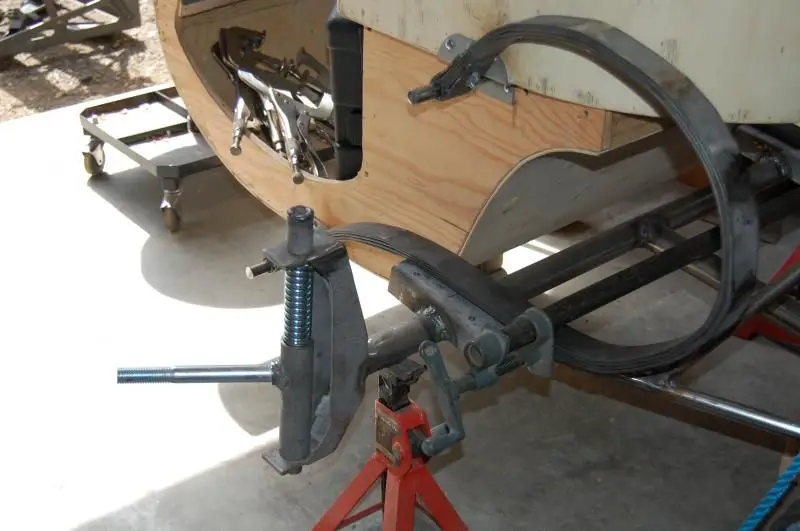