Norman
LORD VADER Moderator
the spindle is bored the bearing fit nice and tight. I bored a through hole in the spindle for a draw bar when needed on a milling bit. So I have a basic milling machine, well sort of now to make the drive train for this. Even at this early stage of building this the mill has made it's own hole for the spindle head and the hole for the draw bar. Once the drive train is made. I'll build the mill's compound slide, then I'll be able to made most all of the parts for the mill by using the mill to machine it's own parts.
the mill's spindle is in place and now boring the through hole in the spindle for a draw bar to hold to hold a cutting bit
boring through the spindle this will latter be bored to 5/8" for a boring bit. it will be bored to a depth of 1"
using the shaper's power train to power the mill.
Next thing to build is the power train for the mill so off to the man cave.
the mill's spindle is in place and now boring the through hole in the spindle for a draw bar to hold to hold a cutting bit
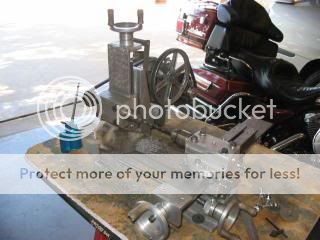
boring through the spindle this will latter be bored to 5/8" for a boring bit. it will be bored to a depth of 1"
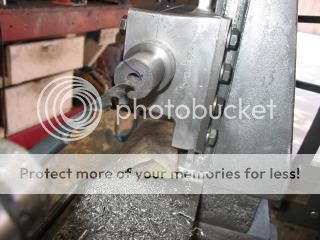
using the shaper's power train to power the mill.
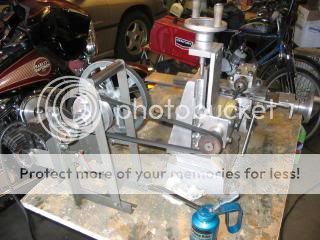
Next thing to build is the power train for the mill so off to the man cave.