Flügelwagen
New Member
If you're like me, you think that the old-school springer forks look cool. A hundred years ago forks of this overall design were seen on on a lot of cool old brands like Excelsior or this Cleveland;
The forks we can get now that look like this are handsome, light, handle bumps pretty good, but are lousy in a turn. I learned this the hard-way while racing at Grange earlier this year. The fork did a poor job of keeping the wheel in line when facing lateral pressure (such as when banking) or even turning the neck when parked! Why is this the case? Well it appears to be because there is too-much slop, too many ways for the parts to shift in the XY plane, and twist about the X-axis.
I'm not willing to walk away from these forks. Let's see if they can be improved with a bit of modification.
Old and worn, or cheaper forks may have have an enlarged hole where the center-screw rubs inside the pinched part of the larger, curved tubing which also results in play about the X axis. Also, because there are four floating fork-legs with slotted holes the axle and the fork crown do a poor job of preventing the fork from paralellagramming or twisting opposite ways on the left and right sides. To eliminate the twist I added a bit of 7/8" fish-mouthed tubing below the center-screw spot, checking to make sure it had clearance between the bottom of the steerer and my 24" tires (there may not be room to do this if you are running 26" wheels).
Okay, that got rid of the twist, now what about the bored out center-screw holes? I found that 1/2" tubing (the kind with the red paint on the ends that is available at the hardware store) is a good fit over the 3/8" center-screw. I wanted the fork to fit over 3" tires, so I welded a short segment of the tubing over the right center-screw hole and purchased a longer, heavy-duty 3/8" bolt. This also makes room for your disk-brake on the left side, but can affect the tracking/balance of your bike by shifting the front wheel to the right. If I was not going oversize with the tires or running a disk-brake, a better way might be to drill the holes out to 1/2" and set the tubing in there flush before welding. Also, because I am making the entire fork wider, I will now have to mount the top of the legs to the outside of the crown instead of the inside.
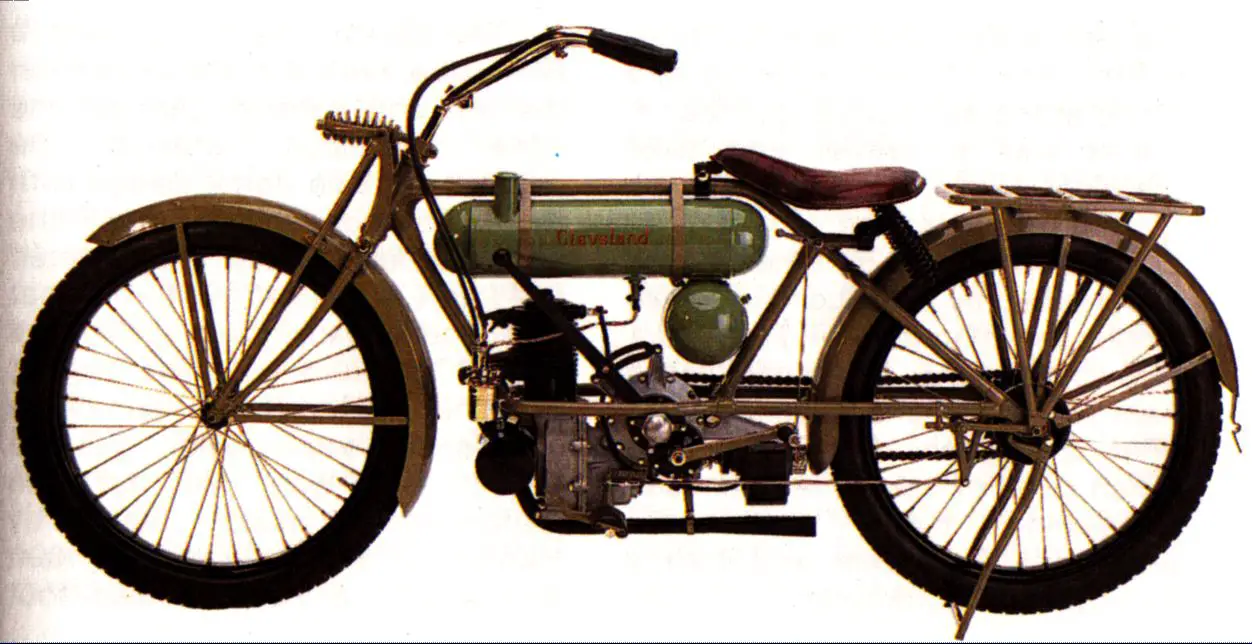
The forks we can get now that look like this are handsome, light, handle bumps pretty good, but are lousy in a turn. I learned this the hard-way while racing at Grange earlier this year. The fork did a poor job of keeping the wheel in line when facing lateral pressure (such as when banking) or even turning the neck when parked! Why is this the case? Well it appears to be because there is too-much slop, too many ways for the parts to shift in the XY plane, and twist about the X-axis.

I'm not willing to walk away from these forks. Let's see if they can be improved with a bit of modification.
Old and worn, or cheaper forks may have have an enlarged hole where the center-screw rubs inside the pinched part of the larger, curved tubing which also results in play about the X axis. Also, because there are four floating fork-legs with slotted holes the axle and the fork crown do a poor job of preventing the fork from paralellagramming or twisting opposite ways on the left and right sides. To eliminate the twist I added a bit of 7/8" fish-mouthed tubing below the center-screw spot, checking to make sure it had clearance between the bottom of the steerer and my 24" tires (there may not be room to do this if you are running 26" wheels).

Okay, that got rid of the twist, now what about the bored out center-screw holes? I found that 1/2" tubing (the kind with the red paint on the ends that is available at the hardware store) is a good fit over the 3/8" center-screw. I wanted the fork to fit over 3" tires, so I welded a short segment of the tubing over the right center-screw hole and purchased a longer, heavy-duty 3/8" bolt. This also makes room for your disk-brake on the left side, but can affect the tracking/balance of your bike by shifting the front wheel to the right. If I was not going oversize with the tires or running a disk-brake, a better way might be to drill the holes out to 1/2" and set the tubing in there flush before welding. Also, because I am making the entire fork wider, I will now have to mount the top of the legs to the outside of the crown instead of the inside.