HYDRAULIC TUBE BENDER - SOME OF MY FINDINGS...
Spent a couple of hours yesterday familiarizing myself with my newly acquired bender.
Whilst waiting for it to be delivered I'd already spent time watching umpteen youtube videos showing this tool in use. First up, what comes across loud and clear from those who know about these things is that this tool is a PIPE bender - not a TUBE bender. They stress there IS a difference. The main difference to be aware of is that PIPE and TUBE diameter measurements differ, in that PIPE is specified according to its
internal diameter and TUBE is specified according to its
external diameter. It's important you're aware of this prior to laying out for the tool - mainly because the five different bend radius dies supplied with the bender are sized for PIPE,
not TUBE. Oh, and the tool is specifically designed to bend malleable steel pipe. If you've reached this point without yawning, read on...
Of all the youtube vids I watched, one in particular grabbed my attention 'cause it outlined and addressed the problems any purchaser of this bender is likely to come up against if they want to use it for bending tube. Or in my case, 24.5mm (1") dia. 6061 aluminium tube. This guy's youtube vid showed how he recommended modifying one of the smaller diameter dies to accommodate the nearest available sized tube. To clarify, the die intended for bending 1" PIPE is
way oversized for 1" tube. So is the 3/4" die. The 1/2" die was closest to being the correct die for bending my 1" aluminium tube, being marginally undersized to allow the tube to snug right down in the die's channel. The youtube guy recommended opening-up the die's channel a little and gently chamferring/rounding the channel edges so it didn't bite into the tube's surface. Following his tips, I planned on doing this - but first I planned on making a few test bends just to get the hang of operating the bender. Unsurprisingly, I've learned practice is the secret. Don't expect to get results right out of the traps.
Probably best to refer to the pics below. First pic shows the first bend I made. Disaster, or what!? Oh yeah, the tool has it's limitations - and I reached them pretty early on doing this bend. I just put the tube in the bender, cranked away at the pump handle a few times, and CRACK! What radius bend is that? About 15 degrees before the alloy tube well and truly cracked. Yeah, that's what'll inevitably occur if you don't take it easy and in stages. And notice the gouge in the tube's sides where the raw edges of the die bit in.
Second pic shows how I modified the 1/2" die so it accommodated the 1" aluminium tube I'm using. I used an abrasive ball in a power drill to clean out and enlarge the channel marginally then I rounded-off the channel's sharp edges so the tube was a snug fit into the die. Compare this modified die to the 3/4" die alongside to see the difference.
Third pic shows how I began bending the frame's curved downtube - but sadly, even this ended up failing when I was just short of completing the bottom bend. SH-----T!!! That was nearly two hours worth of bending - a degree or two at a time - using the segmented marks I'd made on the tube as guides when the tube was placed in the bender. I must have had the tube in and out of the bender 50 times while performing that bend. It's just I got cocky at the last minute and cranked the pump handle a few too many times in my eagerness with the end of the bend in sight. I won't make that mistake next time.
Fourth pic is a close-up showing the downtube's fracture. Because the tube is a snug fit in my modified die, it generally maintains its shape without deforming or creasing at the bend's inner radius. The crack failure occurs on the most stressed area of the bend, it's outer radius. That's because aluminium is nowhere near as malleable as the steel tube intended for use with this bender.
Later this afternoon I'm up for re-attempting a mk2 version of that pesky downtube. And the upper bend will definitely have to be smoothed out some. It definitely won't form as sharp as I've drawn it. Gentle bends are the secret. Stay tuned to find out how I get on. Finger's crossed....
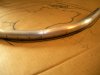