Davezilla
New Member
Just thought I'd make a post to record my frame repair job in progress... This all stemmed from last weekend when I was at the shop and wanted to do a few last minute welds, then the intention was to take everything off the frame, clean it up, strip off the paint and give it a real paint job... So much for that idea...
i got the engine out and wanted to finish welding up my bottom forward mount setup I came up with when I first put the engine on the bike... The lower tube is oval shaped and needed some extra long mount studs going to a flimsy kit bracket and this wasn't working so well... it bent the studs after a few short rides and the engine would not sit rigid in the frame... Totally unacceptable... Sooo... I came up with the idea to sit the engine directly on the frame, then mark where it was sitting and cut a slot at each mark, then I slid a 1" wide 1/8" thick piece of steel thru the slots and bolted the engine to this. This worked great and made the engine very rigid once all bolts were bolted down. I liked it, but needed to weld it to the frame. I just tack welded it during the assembly process and it held so well I didn't bother going back to weld this in. i was planning to take the bike all the way apart anyway for paint and was gonna weld it then... And it worked so well during testing that I just left it as is until I had the time to take the bike apart again.
Anyway... I reached that point last weekend and found a crack starting to grow at one of the corners of one of the slots... I remove the stud and jam nuts from the mount, move the wiring out of the way, and grab my little Mig welder with the amps set on low and wire speed set at about 3... pull the trigger, and blew a hole in the frame... WTF??!! How did That happen so easy?? Now I'm forced to pull the engine, the wiring, and grind out the tack welds that held my mount in the frame, remove the steel mount bracket, and decide how to fix this...
Here's how it looked after some of the damage was cut out... I was gonna just put in some fresh metal, reenforce the area, and weld it all up... but... when cutting into the tubing I notice it's only about .040" thick... Now THAT explains why the welder blew a hole so easily...
Here are a few other pics taken last week...
As you can see, the wall thickness is really thin on this tube... I decided to cut it out and weld in some fresh metal... Of course, this also gives me an excuse to buy a tubing notcher to go with my new pipe bender... I did cut out the bad section of frame today, but need to do some more trimming but leave a little behind to give me some more surface to weld on... I'll definitely be using the TIG welder for this part, I want as much control as possible here...
Here's the bike with the lower tube cut out... for the most part, I'll be cutting the rest of it back even further before any welding will take place... And I need to make time to get to the welder's supply place and refill my argon bottle again... Nothing worse than starting a job and running out of gas in the middle of a weld...
i got the engine out and wanted to finish welding up my bottom forward mount setup I came up with when I first put the engine on the bike... The lower tube is oval shaped and needed some extra long mount studs going to a flimsy kit bracket and this wasn't working so well... it bent the studs after a few short rides and the engine would not sit rigid in the frame... Totally unacceptable... Sooo... I came up with the idea to sit the engine directly on the frame, then mark where it was sitting and cut a slot at each mark, then I slid a 1" wide 1/8" thick piece of steel thru the slots and bolted the engine to this. This worked great and made the engine very rigid once all bolts were bolted down. I liked it, but needed to weld it to the frame. I just tack welded it during the assembly process and it held so well I didn't bother going back to weld this in. i was planning to take the bike all the way apart anyway for paint and was gonna weld it then... And it worked so well during testing that I just left it as is until I had the time to take the bike apart again.
Anyway... I reached that point last weekend and found a crack starting to grow at one of the corners of one of the slots... I remove the stud and jam nuts from the mount, move the wiring out of the way, and grab my little Mig welder with the amps set on low and wire speed set at about 3... pull the trigger, and blew a hole in the frame... WTF??!! How did That happen so easy?? Now I'm forced to pull the engine, the wiring, and grind out the tack welds that held my mount in the frame, remove the steel mount bracket, and decide how to fix this...
Here's how it looked after some of the damage was cut out... I was gonna just put in some fresh metal, reenforce the area, and weld it all up... but... when cutting into the tubing I notice it's only about .040" thick... Now THAT explains why the welder blew a hole so easily...
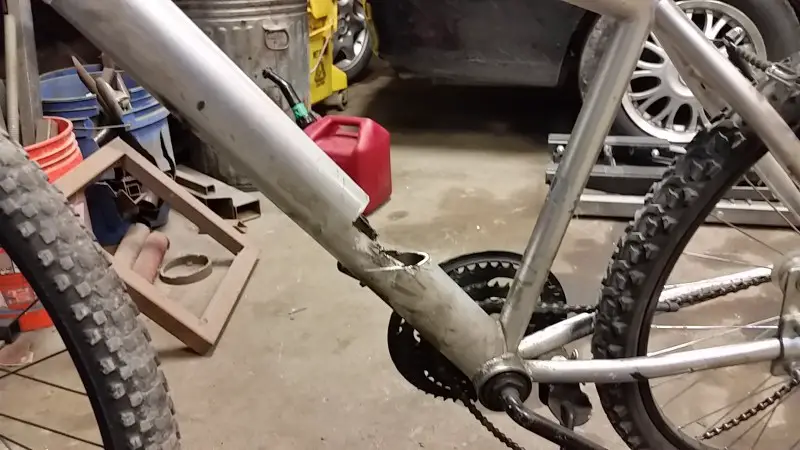
Here are a few other pics taken last week...
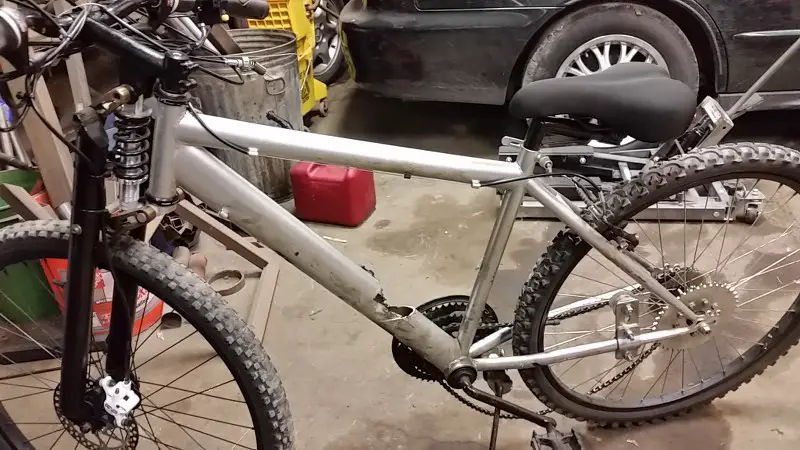
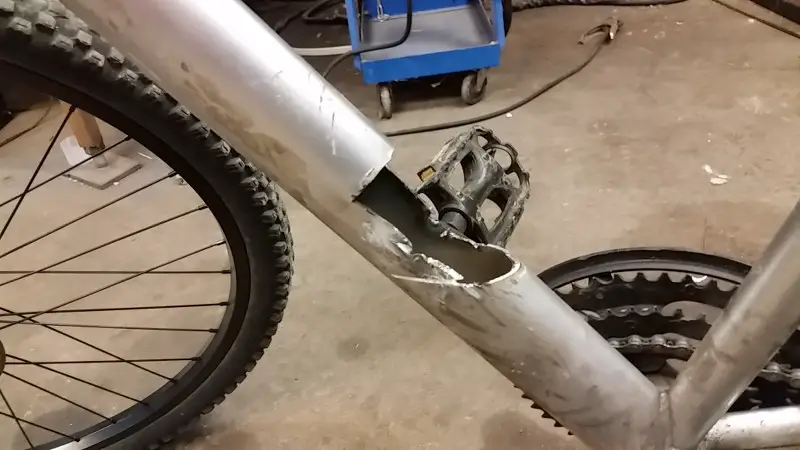
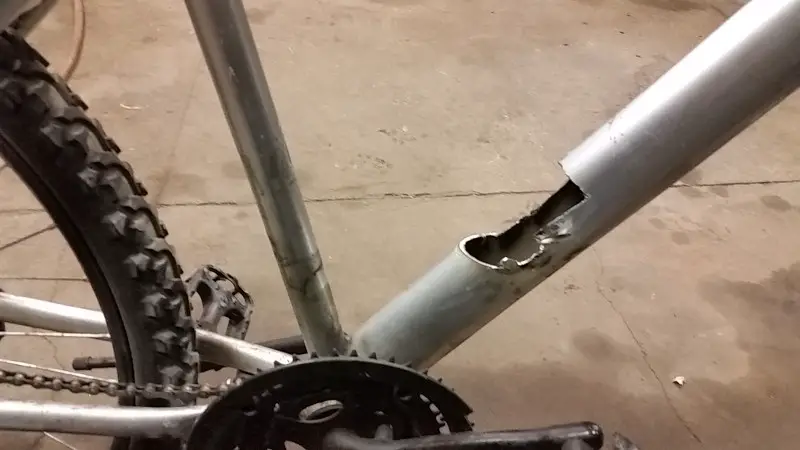
As you can see, the wall thickness is really thin on this tube... I decided to cut it out and weld in some fresh metal... Of course, this also gives me an excuse to buy a tubing notcher to go with my new pipe bender... I did cut out the bad section of frame today, but need to do some more trimming but leave a little behind to give me some more surface to weld on... I'll definitely be using the TIG welder for this part, I want as much control as possible here...
Here's the bike with the lower tube cut out... for the most part, I'll be cutting the rest of it back even further before any welding will take place... And I need to make time to get to the welder's supply place and refill my argon bottle again... Nothing worse than starting a job and running out of gas in the middle of a weld...
