bluegoatwoods
Active Member
I've just about perfected a way of making good, stout brackets for mounting to frame tubes, chainstays, etc.
I can imagine a number of uses for fastening stuff to the bike. Cargo racks, cable & wire mounts, stuff like that. Here's an example.
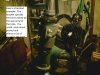
I started with a caliper to measure the diameter of the tube with reasonable accuracy. In the example below one of the tubes was 43 millimeters across. After a bit of experimentation, I decided that the length of the arc I was going to make should be 2.2 times the diameter. So in this case I needed 43mm X 2.2 = about 94 mm. But you need more for the 'ears'. About 25 mm each works well. So you need 94 + (25 X 2)= about 145 mm total.
Now find something round and tough that measures 43mm across.
Sockets work well
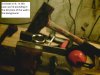
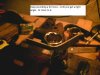
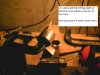
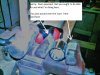
I wouldn't drill the holes you need for mounting until after the bending. Those spots are liable to be a bit weak and might bend there instead of where you want it to.
I can imagine a number of uses for fastening stuff to the bike. Cargo racks, cable & wire mounts, stuff like that. Here's an example.
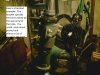
I started with a caliper to measure the diameter of the tube with reasonable accuracy. In the example below one of the tubes was 43 millimeters across. After a bit of experimentation, I decided that the length of the arc I was going to make should be 2.2 times the diameter. So in this case I needed 43mm X 2.2 = about 94 mm. But you need more for the 'ears'. About 25 mm each works well. So you need 94 + (25 X 2)= about 145 mm total.
Now find something round and tough that measures 43mm across.
Sockets work well
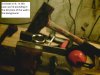
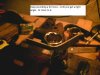
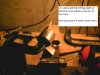
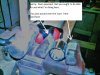
I wouldn't drill the holes you need for mounting until after the bending. Those spots are liable to be a bit weak and might bend there instead of where you want it to.