foureasy
New Member
i will periodically add pictures and the reasons why, for a few of the things that i have done in the quest for speed.
i did this to my combustion chamber to make it a more efficient "squish" type chamber. it helps to promote a more even flame travel and less risk of detonation. not to mention the added benefits of increased compression. the ideal size of the squish band is 1/2 of the bore area, which i have come pretty close to.
weld it up
face it and grind it out
i got five on it
i did this to my combustion chamber to make it a more efficient "squish" type chamber. it helps to promote a more even flame travel and less risk of detonation. not to mention the added benefits of increased compression. the ideal size of the squish band is 1/2 of the bore area, which i have come pretty close to.
weld it up
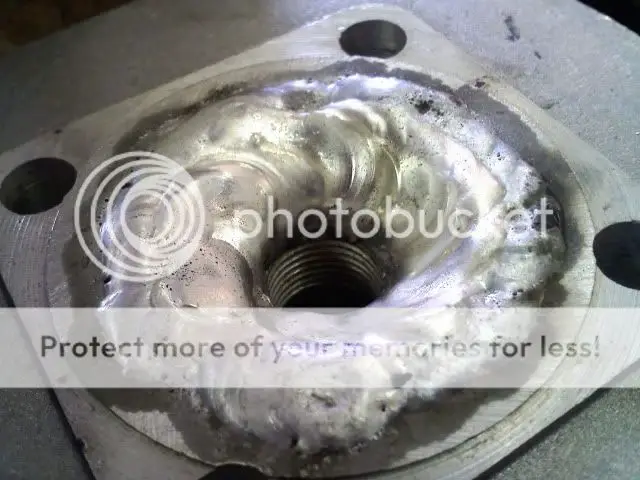
face it and grind it out
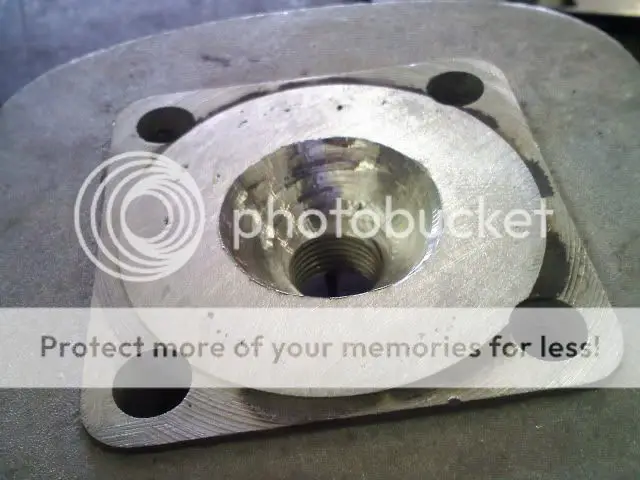
i got five on it
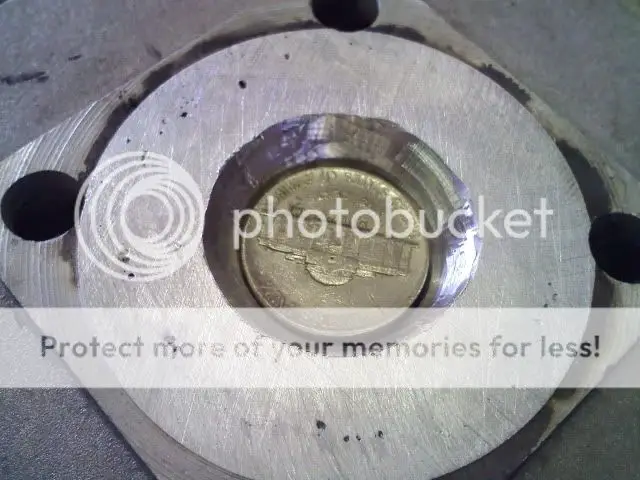