sissytrikerider
New Member
as im sure this will work with any 1" threaded fork with any other bicycle using the 1 1/8" zero stack (zs) head set as in my skyhawk gt2as frame and I would assume any variant of this frame. I searched various possibilities for the correct headset or shim or what ever it may be. the problem is that the hole in the bearing cup provided with the bike for the fork to pass through is to big. The correct head set according to the standardized headset identification system [s.h.i.s] would be is a zs44/25.4-zs44/26 is not available. The 1" threaded fork (which was standard until someone decided to make it not) used an exposed bearing cup (ec). now some manufactures use the same cup size for the 1 1/8" and 1" headsets and just the race which presses into the frame varies. My choice of headset (1") was by crane creek and is a sealed set up using a o-ring to keep out the crud and uses the 1 1/8" ball bearing set up so I came up with this inexpensive fix to share with the MB gang.
1- source a piece of 1in copper tubing and a couple of 1in copper couplings. with no stops. Now I happen to be a proud licensed non-union (yup I went there) plumber and happen to have abundance of worthless scrap copper tubing on hand to select from (please buy more china bike stuff and support your china economy to get them thriving again and bring the price of scrap up)

2-gather tools required. I used air tools, one with a sanding drum on an arbor from hf, one with a deburing bit, your 1" head set of choice, the bearing cups from the bike (one in pic but you will need both ) and solder tools. (brushes, torch, sand tape ect)

3-open the hole in the bearing cups so that the copper coupling fits sung through the hole with the sanding drum. this did not take much in my case as the sizes were very close, but take your time and be sure to take "material off" all around the opening to keep the end result centered.
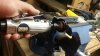
4- ream any edge from the inside of the copper pipe from your method of cutting, in my case was from a tubing cutter. solder one coupling flush to the end of the tubing, I soldered one end, the end away from the edge of the pipe.
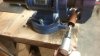
1- source a piece of 1in copper tubing and a couple of 1in copper couplings. with no stops. Now I happen to be a proud licensed non-union (yup I went there) plumber and happen to have abundance of worthless scrap copper tubing on hand to select from (please buy more china bike stuff and support your china economy to get them thriving again and bring the price of scrap up)

2-gather tools required. I used air tools, one with a sanding drum on an arbor from hf, one with a deburing bit, your 1" head set of choice, the bearing cups from the bike (one in pic but you will need both ) and solder tools. (brushes, torch, sand tape ect)

3-open the hole in the bearing cups so that the copper coupling fits sung through the hole with the sanding drum. this did not take much in my case as the sizes were very close, but take your time and be sure to take "material off" all around the opening to keep the end result centered.
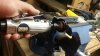
4- ream any edge from the inside of the copper pipe from your method of cutting, in my case was from a tubing cutter. solder one coupling flush to the end of the tubing, I soldered one end, the end away from the edge of the pipe.
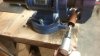
Last edited: