Hi All,
Just thought I'd join the forum and mention the project I've been working on - So here's my first post.
Around Christmas time, I rescued an old petrol bike from a pile of rubbish and rebuilt it, and it's quite a nice bike, but wanted something electric without the range limitations of batteries, so I built my own small-size generator after a few experiments and proof-of-concepts and finally built a prototype and tested it.
The generator was made by coupling a 300w motor to a small 4-stroke engine and using this both to start the motor ( pull start still worked ) and to produce power. All the flanges and shaft components were 3D printed in ABS. 300w isn't much, but the legal limit here in Australia is 200w, so it seemed enough.
After that, I needed an electric bicycle and so set about making one with a 500w 48v kit downrated to 24v.
Testing on the bench seemed to work OK, and so I developed an autothrottle controller to adjust the engine output power to maintain a particular voltage out of the generator, allowing for charging the batteries while in operation. Two SLA batteries provided the power for the motor, and the sink for charging. As voltage from the battery dropped under load, the engine power is increased, with a 1v hysteresis around 24.5 to 25.5 volts ( at least for the test setup ) - This allowed some charging of the battery while providing enough surplus power for the bicycle.
I cleaned up the battery holders, and used a framework of ABS brackets and 1/2" nylon straps to hold everything together. The batteries are in solid and don't move and the transistors of the controller heatsink into the bike frame as well.
A picture of the CAD diagrams for the battery holder components -
That was the MK I. I did ride around on it and finally collected some good operational data on it. The mileage was about 51km/l ( about 130 mpg ) including charging the battery while riding, but eventually the generator failed as it wasn't actually able to deal with the sorts of currents it was supposed to be designed for - Still, I got some good results and the combination of electric and petrol was perfect. No charging needed, can autostart and noise is directly related to power. The volume would go up slowly and then come down instantly that I released the throttle, though being electric, the batteries took up the slack in between. Also, the torque was available from standstill, so I didn't have to worry about pedaling to start - just throttle up and off - Also much better torque up hills.
Anyway, so far I am really happy with the outcome and am working on the MK II version, which should be even lighter, and have the capability to run full battery charge as well as power the bike, while running lights at the same time.
Regards
David.
Just thought I'd join the forum and mention the project I've been working on - So here's my first post.
Around Christmas time, I rescued an old petrol bike from a pile of rubbish and rebuilt it, and it's quite a nice bike, but wanted something electric without the range limitations of batteries, so I built my own small-size generator after a few experiments and proof-of-concepts and finally built a prototype and tested it.
The generator was made by coupling a 300w motor to a small 4-stroke engine and using this both to start the motor ( pull start still worked ) and to produce power. All the flanges and shaft components were 3D printed in ABS. 300w isn't much, but the legal limit here in Australia is 200w, so it seemed enough.
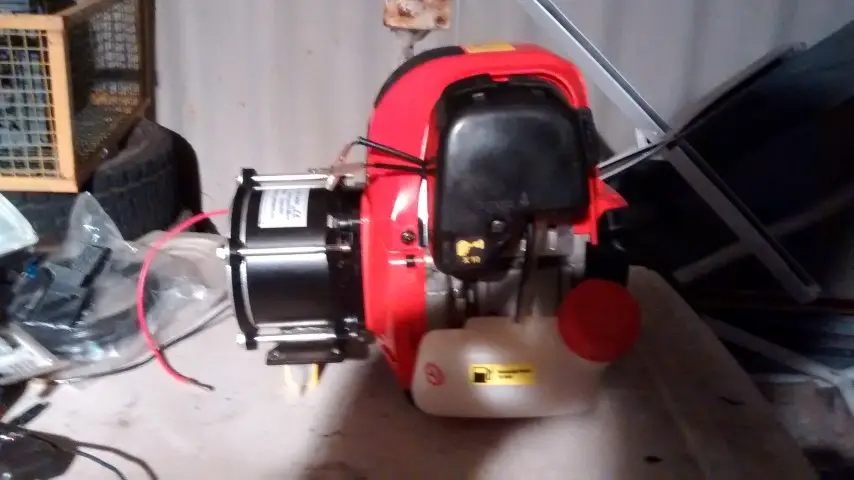
After that, I needed an electric bicycle and so set about making one with a 500w 48v kit downrated to 24v.
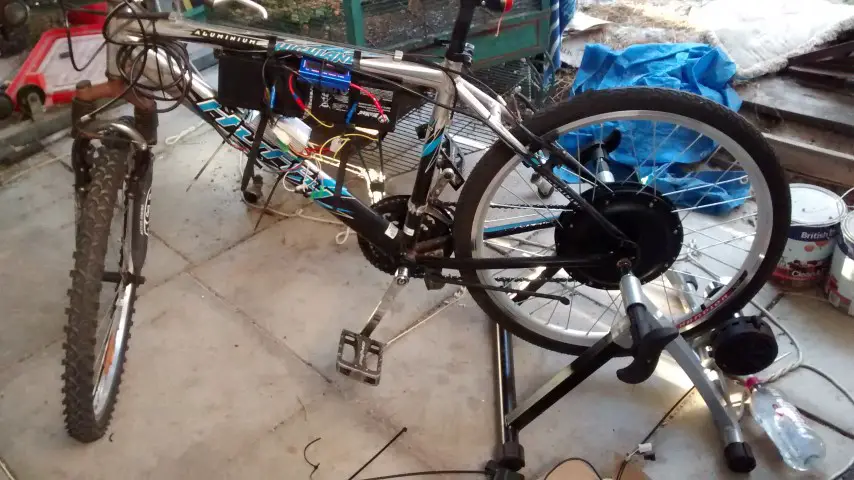
Testing on the bench seemed to work OK, and so I developed an autothrottle controller to adjust the engine output power to maintain a particular voltage out of the generator, allowing for charging the batteries while in operation. Two SLA batteries provided the power for the motor, and the sink for charging. As voltage from the battery dropped under load, the engine power is increased, with a 1v hysteresis around 24.5 to 25.5 volts ( at least for the test setup ) - This allowed some charging of the battery while providing enough surplus power for the bicycle.
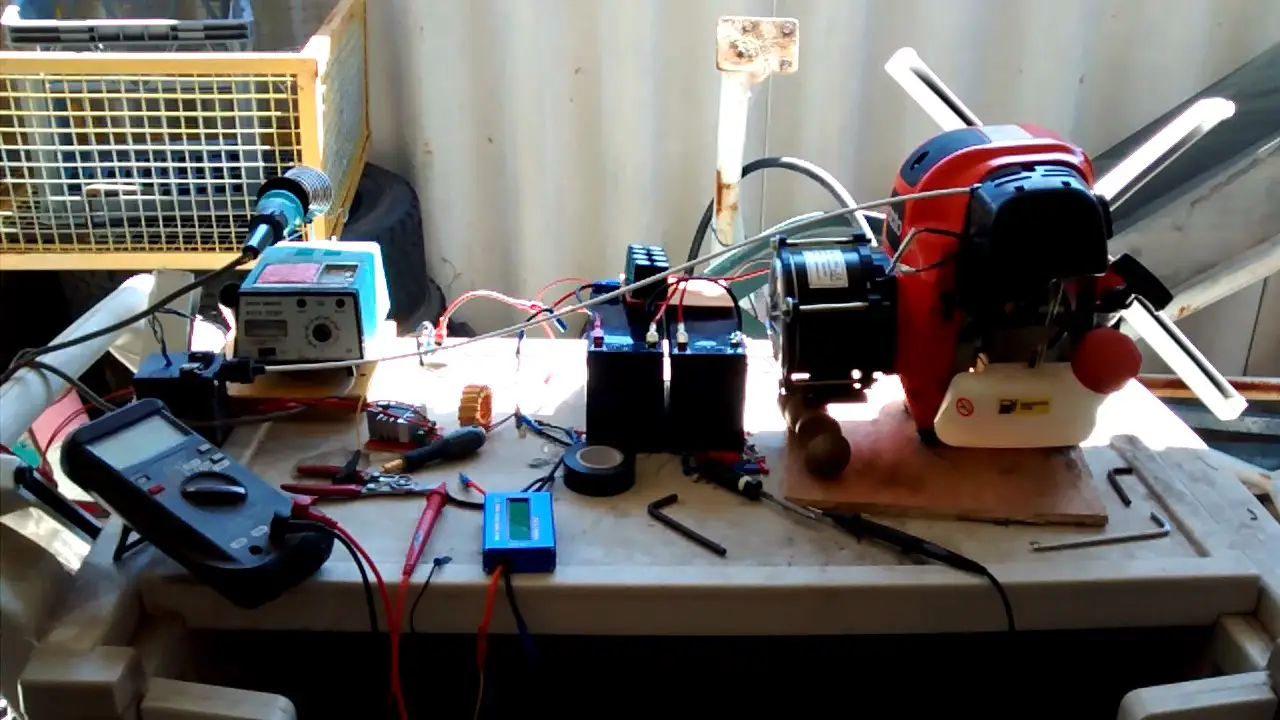
I cleaned up the battery holders, and used a framework of ABS brackets and 1/2" nylon straps to hold everything together. The batteries are in solid and don't move and the transistors of the controller heatsink into the bike frame as well.
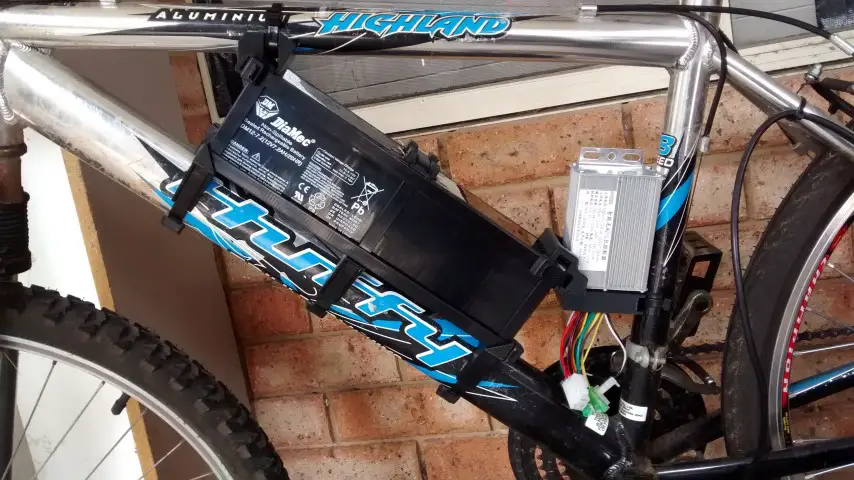
A picture of the CAD diagrams for the battery holder components -
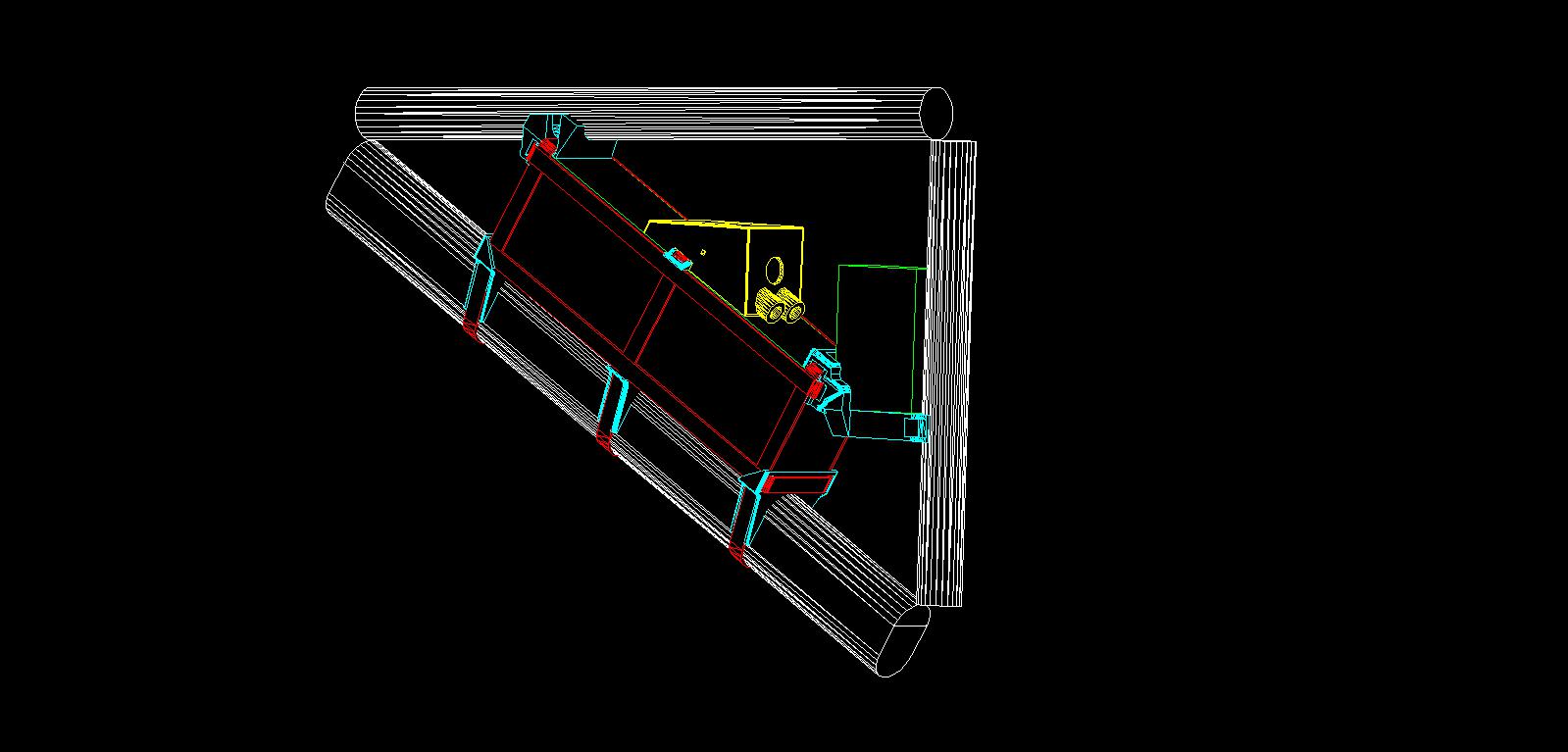
That was the MK I. I did ride around on it and finally collected some good operational data on it. The mileage was about 51km/l ( about 130 mpg ) including charging the battery while riding, but eventually the generator failed as it wasn't actually able to deal with the sorts of currents it was supposed to be designed for - Still, I got some good results and the combination of electric and petrol was perfect. No charging needed, can autostart and noise is directly related to power. The volume would go up slowly and then come down instantly that I released the throttle, though being electric, the batteries took up the slack in between. Also, the torque was available from standstill, so I didn't have to worry about pedaling to start - just throttle up and off - Also much better torque up hills.
Anyway, so far I am really happy with the outcome and am working on the MK II version, which should be even lighter, and have the capability to run full battery charge as well as power the bike, while running lights at the same time.
Regards
David.