Well, sometimes old school materials just do the job. He experimented with everything possible to use for a drive roller. The problem is to get something that doesn't slip when wet and doesn't wear the tire. Turns out that hardwood works better than all other materials that he worked with.
Myself, I made a knurled steel roller that worked very well wet until the knurls quickly smoothed themselvs down.
A plain steel roller works excellent when dry, and still works wet if you're careful with the throttle.
I did experiment with a grindstone roller. It never slipped even in muddy roads, but the tire wore out in about 100 miles.
The most important thing you can do to make a friction drive work more effectivly and efficently is to use as large of diameter roller that you can get away with.
I would discard the spring loaded rack idea, and figure out a way to mechanicaly adjust the rack for roller pressure. Maybe a couple of turnbuckels attached to struts at the rear of the rack? Spring loaded like your drawing, will allow the engine and rack to bounce around on road bumps, and prolly just the weight of the whole assembly will depress the roller too much. On my 3.5" roller I never needed any more than 3/16" tire deflection with the smooth roller for good grip.
Myself, I made a knurled steel roller that worked very well wet until the knurls quickly smoothed themselvs down.
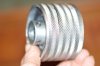
A plain steel roller works excellent when dry, and still works wet if you're careful with the throttle.
I did experiment with a grindstone roller. It never slipped even in muddy roads, but the tire wore out in about 100 miles.
The most important thing you can do to make a friction drive work more effectivly and efficently is to use as large of diameter roller that you can get away with.
I would discard the spring loaded rack idea, and figure out a way to mechanicaly adjust the rack for roller pressure. Maybe a couple of turnbuckels attached to struts at the rear of the rack? Spring loaded like your drawing, will allow the engine and rack to bounce around on road bumps, and prolly just the weight of the whole assembly will depress the roller too much. On my 3.5" roller I never needed any more than 3/16" tire deflection with the smooth roller for good grip.
Last edited: