Hey Tom, it’s a Paughco 2.2 gallon tank, unpainted. I got it off ebay, but it’s listed elsewhere, too:
http://www.amazon.com/PAUGHCO-GAS-T...8&qid=1432854499&sr=8-1&keywords=paughco+tank
http://www.paughco.com/2008-catalog...anks For Universal Applications (page 1).html
I’m a little shocked by those prices; mine was WAY cheaper than the current prices on those sites. Guess it was a good move to get it back then, even if I do have to sand the rust off before I paint it.
Put yesterday towards welding the freewheel roller ramp to the back axle, welding the roller ramp tube to the hub, and then welding the new lips onto the front forks. So the front wheel is on. It spins nicely, but the bearings rattle a little, so if an opportunity presents itself I might try to replace them. Also welded the extra steel rods into place inside the forks. Then marked out where I want to mount the engine on the skidplate (wiggling it around and judging by eye, which will probably come back to haunt me) and then made a paper template of the bolt pattern. Cut out the template and taped it into the footprint I’d marked on the skidplate, so the holes are ready to center-punch and drill out. I’ll lathe a little jig to center the punch on the template’s circle outline, and then onwards to drilling out the holes and finally mounting the engine!
Today I made a new cap for the thin side of the front axle, and machined bolt holes in the caps for the front and back axles. Assembled the freewheel to make sure it all fit together. Just need to lengthen the spacing collar between the hub and the roller by about 0.2” and then everything should spin freely. Dandy.
Still don’t know if the freewheel even works yet, since I haven’t cut the rollers from the rod stock. Could do that with my angle grinder, but can do it properly on the lathe tomorrow so that’s better.
There’s a wobble on the rear 51T sprocket. I think the sprocket itself is warped, because I cut out the mount for it on a water jet saw— so it should be perfect. I’ll have to look very closely at the sprocket to be sure, but I might be in the market for a new one… How much wobble can I tolerate? I know a chain can bend a little sideways, but I don’t want to make it do any more stretching than it has to, considering that the sprockets probably won’t be perfectly aligned anyhow. Either way, I’ll use the slightest of tack-welds to connect the sprocket mount to the freewheel roller in case I need to make a new one!
Gonna be a short day in the shop tomorrow, maybe just two hours, so it will be tough to get everything done. Shop’s closed on the weekends, so the transmission isn’t going to be done until next week. The jackshaft clutch is the weak link in the whole system now, plenty could go wrong there. But at least a clutch is something that can be purchased off the shelf ready to go, if it comes to that.
rig
http://www.amazon.com/PAUGHCO-GAS-T...8&qid=1432854499&sr=8-1&keywords=paughco+tank
http://www.paughco.com/2008-catalog...anks For Universal Applications (page 1).html
I’m a little shocked by those prices; mine was WAY cheaper than the current prices on those sites. Guess it was a good move to get it back then, even if I do have to sand the rust off before I paint it.
Put yesterday towards welding the freewheel roller ramp to the back axle, welding the roller ramp tube to the hub, and then welding the new lips onto the front forks. So the front wheel is on. It spins nicely, but the bearings rattle a little, so if an opportunity presents itself I might try to replace them. Also welded the extra steel rods into place inside the forks. Then marked out where I want to mount the engine on the skidplate (wiggling it around and judging by eye, which will probably come back to haunt me) and then made a paper template of the bolt pattern. Cut out the template and taped it into the footprint I’d marked on the skidplate, so the holes are ready to center-punch and drill out. I’ll lathe a little jig to center the punch on the template’s circle outline, and then onwards to drilling out the holes and finally mounting the engine!
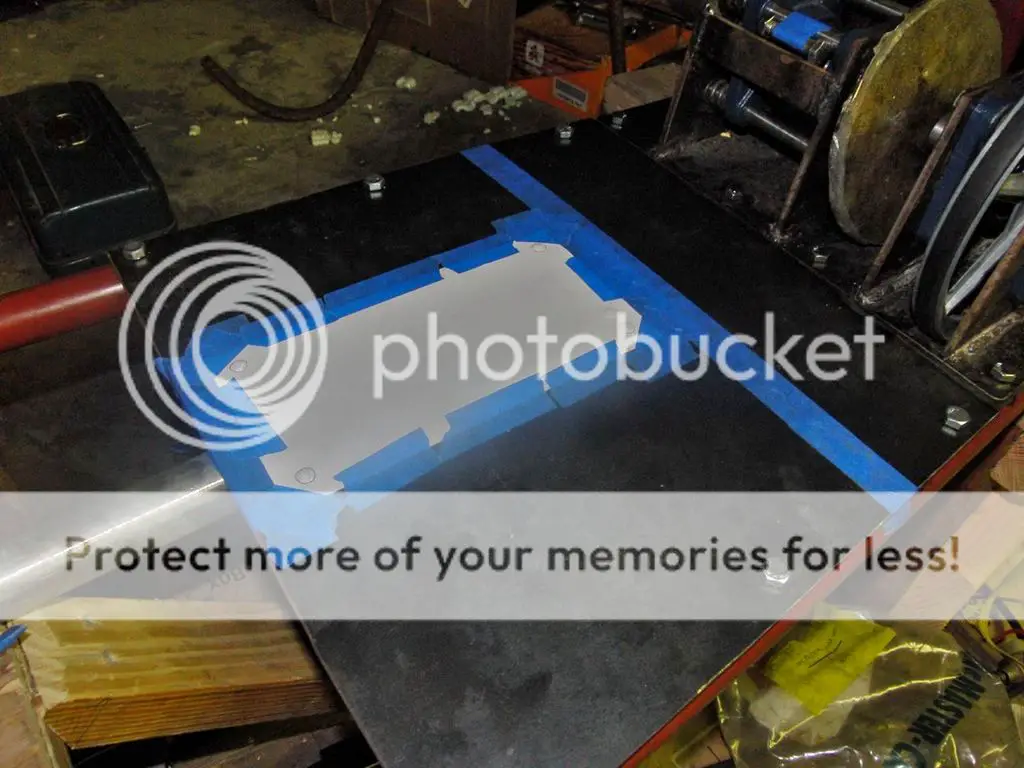
Today I made a new cap for the thin side of the front axle, and machined bolt holes in the caps for the front and back axles. Assembled the freewheel to make sure it all fit together. Just need to lengthen the spacing collar between the hub and the roller by about 0.2” and then everything should spin freely. Dandy.
Still don’t know if the freewheel even works yet, since I haven’t cut the rollers from the rod stock. Could do that with my angle grinder, but can do it properly on the lathe tomorrow so that’s better.
There’s a wobble on the rear 51T sprocket. I think the sprocket itself is warped, because I cut out the mount for it on a water jet saw— so it should be perfect. I’ll have to look very closely at the sprocket to be sure, but I might be in the market for a new one… How much wobble can I tolerate? I know a chain can bend a little sideways, but I don’t want to make it do any more stretching than it has to, considering that the sprockets probably won’t be perfectly aligned anyhow. Either way, I’ll use the slightest of tack-welds to connect the sprocket mount to the freewheel roller in case I need to make a new one!
Gonna be a short day in the shop tomorrow, maybe just two hours, so it will be tough to get everything done. Shop’s closed on the weekends, so the transmission isn’t going to be done until next week. The jackshaft clutch is the weak link in the whole system now, plenty could go wrong there. But at least a clutch is something that can be purchased off the shelf ready to go, if it comes to that.
rig
Last edited: