BarelyAWake
New Member
This is a basic tutorial on how to cut, form & fit the panels for a tank, even if you can't weld - bringing in the finished pieces to your local welding shop will not only get you that in-frame tank ya always wanted, but you'll save a buncha cash in the process;
Buried in the Rustoration Build Off was a request and the resultant rant, I thought I'd dig it outa there for ya. It's a lil weird as there was a buncha other stuff mixed in at the time... but it still may help those unfamiliar with basic sheet metal work. Please feel free to post any questions or comments, tips, suggestions and advice - even where to get tanks ifn ya know a guy.
Gettin' a fuel tank is often a stumbling point preventing some from considering a build they'd like - while you can pay to have one made it's often cost-prohibitive. Most folks without welding equipment wouldn't consider a DIY tank as a possibility, or really know why it costs so much...
It's the time & labor involved in making and fitting the panels that costs the big bucks, even for the most experienced makin' a new shape for the first time as it jus' eats up the hours. With a lil practice & patience you can make those panels and fit them yourself - bring the finished pieces in to a skilled local welder to zot them can save you tons of yer hard-earned pennies, not to mention the braggin' rights in being able to say "I made this FTW!" it also allows you to choose the material you'd like the tank made outa - steel, aluminum, stainless, even copper... although that'd need to be soldered together ofc. A sheet of mild steel is cheap enough, there's no fancy tools beyond a jigsaw, dremel & a coupla files. It's so worth an experiment, the potential outweighs the cost - even if you end up jus' scraping it you've learned a bunch, keep at it and you'll have a unique bike worthy of yer efforts and a valuable skill learned.
Still... somethin' like fabin' a sheet metal tank is both much harder and far easier than you would think... if that sounds strange - just get some thick construction paper (think cereal box, corrugated cardboard won't work well) and make a simple box with some tape holdin' it together. While initially it's easy - any misalignment, dent, crinkle, or gap (particularly in the corners) will skew the whole thing. While the welder can make up for a poor fit somewhat by filling the gaps it'll show up like a sore thumb. Also, the longer you need spend "filling" with molten metal - the more heat is generated and so distortion is inevitable.
So it's all about how well you can get the pieces to fit in the first place - if ya get that down, the welding part is easy for anyone that knows their stuff. Flats and angles are somewhat easier than curves, but the shape is up to you and yer build. With that in mind, it's best to get far more materials than what you'd think would be necessary. Although I'm just cuttin' two side panels at the moment - I got enough sheet steel to make five. Cutting out three to start with I choose the best of the two for the tank - the third I save for experimentation and the rest of the steel I save for when I mess up (notice "when" not "if" lol). It's best to not commit to any one panel till yer done - often it's far easier to just cut out another than to try to "fix" something that went horribly wrong... or even jus' a lil screwy.
I decided to do as much of the tank as possible at home, bringing it in only to be welded to speed up the process a bit and while there's far better tools for it at work, I've simply more time at home to make sure the various panels fit as well as I can manage.
I must say though - getting a 2' x 2' sheet of 20 gauge mild steel home on a MB is... interesting lol
The tank will be about 24"L x 5"W x 3"T with the only real challenge being finding some vented fill cap and base that's about 1 3/4" wide... I'd really like a brass cap but we'll see what I can find. There will be a "fuel sight gauge" made from brass elbows and a hunk of clear fuel line, and ofc copper fuel lines... tho that's not really part of the tank lol
The poor, filthy Schwinn bein' a workhorse;
and the initial measurements bein' figured out fer the tank; (click to view larger, same goes for all lil pics)
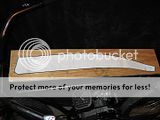
In the pic it looks as if the tracing is off, it isn't - it's just the angle of the pic. There's a 1/4" gap all around the tank to allow for the fasteners BTW
Buried in the Rustoration Build Off was a request and the resultant rant, I thought I'd dig it outa there for ya. It's a lil weird as there was a buncha other stuff mixed in at the time... but it still may help those unfamiliar with basic sheet metal work. Please feel free to post any questions or comments, tips, suggestions and advice - even where to get tanks ifn ya know a guy.

Gettin' a fuel tank is often a stumbling point preventing some from considering a build they'd like - while you can pay to have one made it's often cost-prohibitive. Most folks without welding equipment wouldn't consider a DIY tank as a possibility, or really know why it costs so much...
It's the time & labor involved in making and fitting the panels that costs the big bucks, even for the most experienced makin' a new shape for the first time as it jus' eats up the hours. With a lil practice & patience you can make those panels and fit them yourself - bring the finished pieces in to a skilled local welder to zot them can save you tons of yer hard-earned pennies, not to mention the braggin' rights in being able to say "I made this FTW!" it also allows you to choose the material you'd like the tank made outa - steel, aluminum, stainless, even copper... although that'd need to be soldered together ofc. A sheet of mild steel is cheap enough, there's no fancy tools beyond a jigsaw, dremel & a coupla files. It's so worth an experiment, the potential outweighs the cost - even if you end up jus' scraping it you've learned a bunch, keep at it and you'll have a unique bike worthy of yer efforts and a valuable skill learned.
Still... somethin' like fabin' a sheet metal tank is both much harder and far easier than you would think... if that sounds strange - just get some thick construction paper (think cereal box, corrugated cardboard won't work well) and make a simple box with some tape holdin' it together. While initially it's easy - any misalignment, dent, crinkle, or gap (particularly in the corners) will skew the whole thing. While the welder can make up for a poor fit somewhat by filling the gaps it'll show up like a sore thumb. Also, the longer you need spend "filling" with molten metal - the more heat is generated and so distortion is inevitable.
So it's all about how well you can get the pieces to fit in the first place - if ya get that down, the welding part is easy for anyone that knows their stuff. Flats and angles are somewhat easier than curves, but the shape is up to you and yer build. With that in mind, it's best to get far more materials than what you'd think would be necessary. Although I'm just cuttin' two side panels at the moment - I got enough sheet steel to make five. Cutting out three to start with I choose the best of the two for the tank - the third I save for experimentation and the rest of the steel I save for when I mess up (notice "when" not "if" lol). It's best to not commit to any one panel till yer done - often it's far easier to just cut out another than to try to "fix" something that went horribly wrong... or even jus' a lil screwy.
I decided to do as much of the tank as possible at home, bringing it in only to be welded to speed up the process a bit and while there's far better tools for it at work, I've simply more time at home to make sure the various panels fit as well as I can manage.
I must say though - getting a 2' x 2' sheet of 20 gauge mild steel home on a MB is... interesting lol
The tank will be about 24"L x 5"W x 3"T with the only real challenge being finding some vented fill cap and base that's about 1 3/4" wide... I'd really like a brass cap but we'll see what I can find. There will be a "fuel sight gauge" made from brass elbows and a hunk of clear fuel line, and ofc copper fuel lines... tho that's not really part of the tank lol
The poor, filthy Schwinn bein' a workhorse;
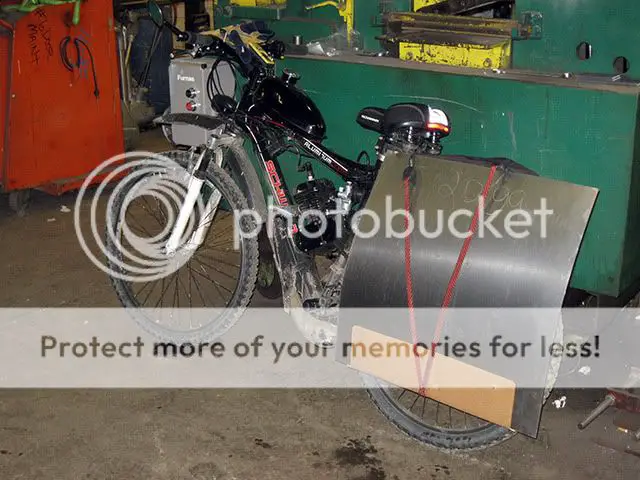
and the initial measurements bein' figured out fer the tank; (click to view larger, same goes for all lil pics)
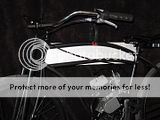
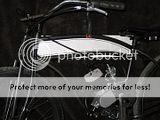
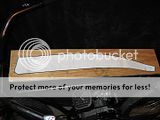
In the pic it looks as if the tracing is off, it isn't - it's just the angle of the pic. There's a 1/4" gap all around the tank to allow for the fasteners BTW
Last edited: